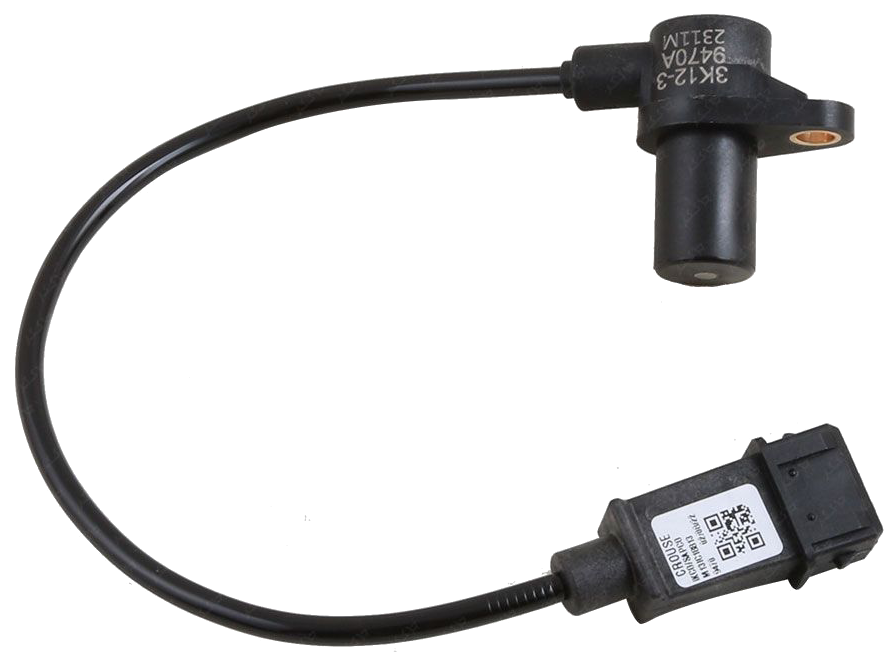
Crankshaft Welding, Resistance Testing And Vision Process
Description
General Crankshaft Sensor Welding Machine
The crankshaft sensor coil is soldered to the phase plate, then the sensor pins are welded to it on the other side.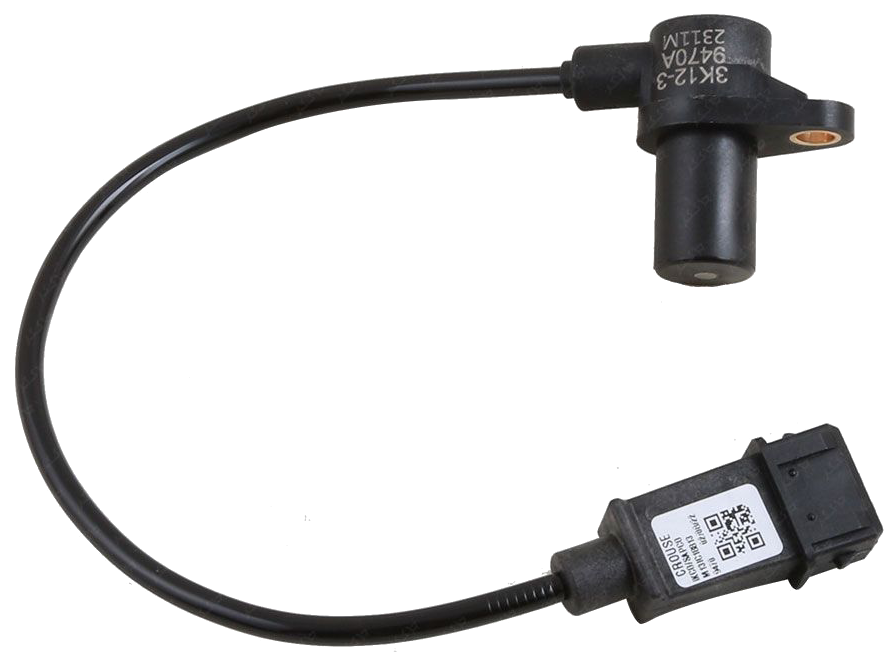
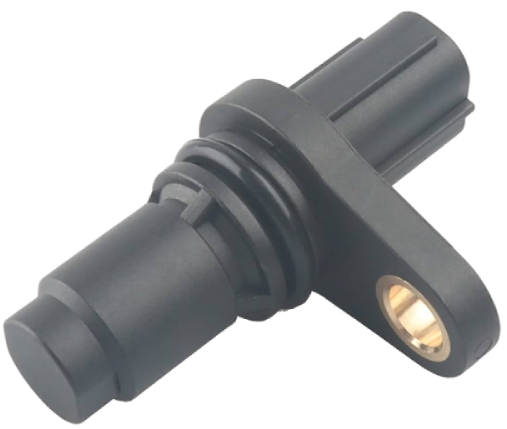
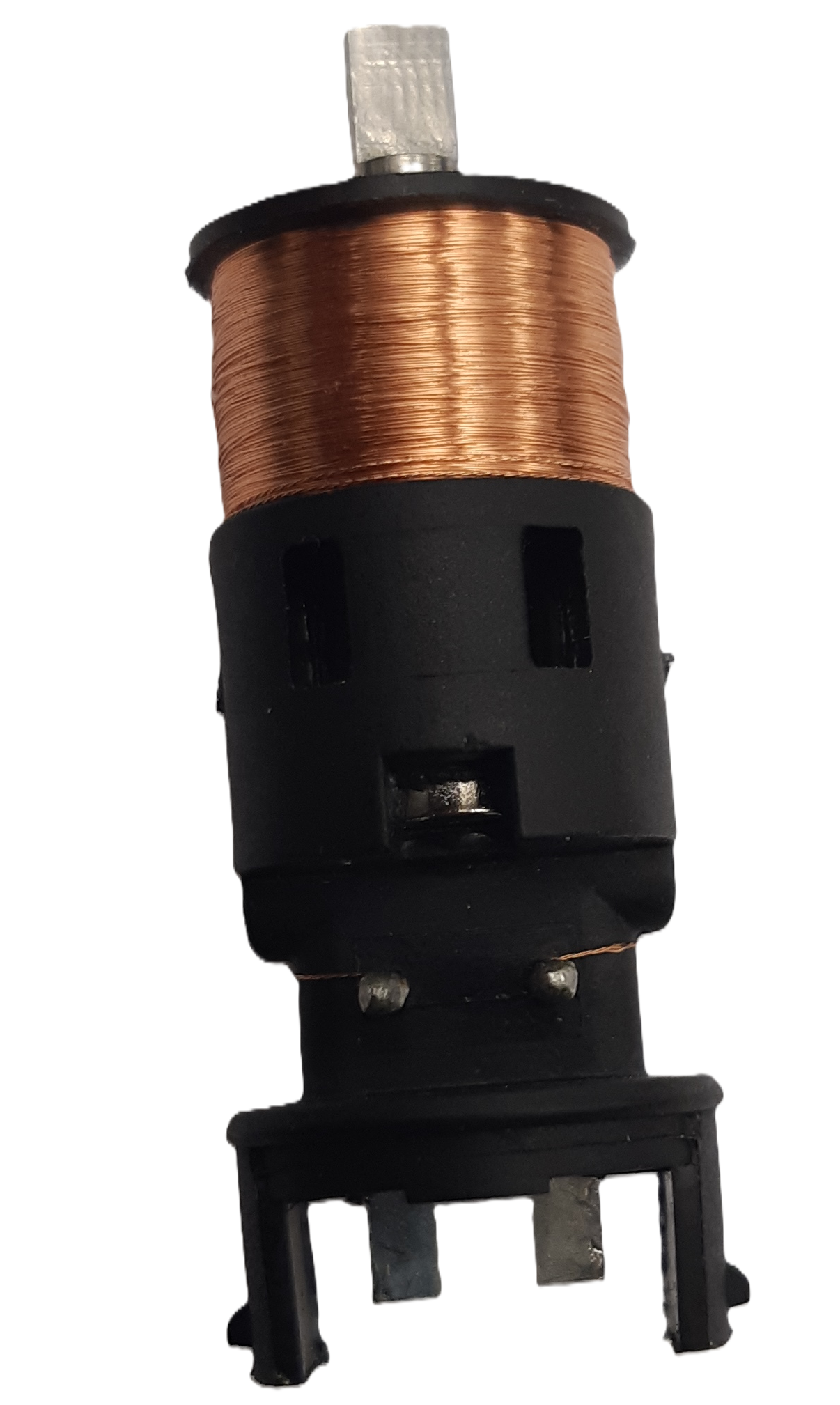
Stages of the work cycle
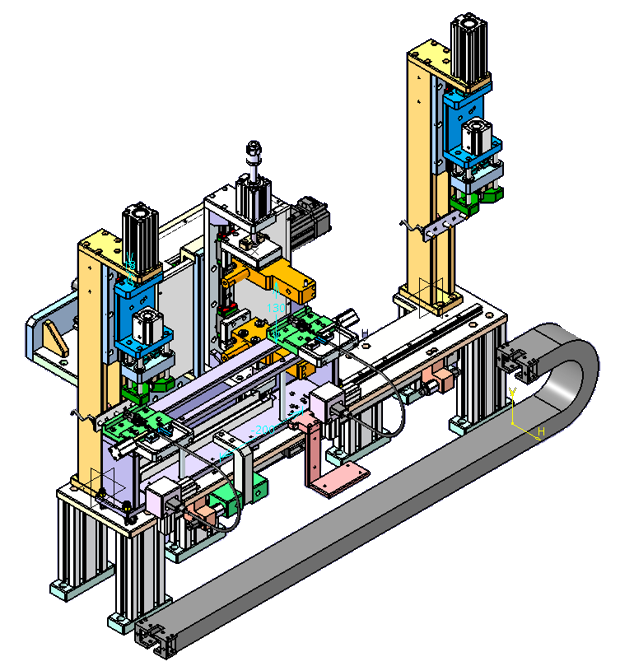
- Insert Part: The part is placed in the machine by the operator..
- Automatic adjustment: Guiding parts through mechanism and software.
- Slide: The slide jack moves the part to the welding area, and on the other side, the welded part is removed and a new part is placed.
- Vision: Performing a vision process to ensure correct placement of parts.
- Weld: Performing the first-level welding process.
- Motion Axis X: Servo axis movement to the next base welding position.
- Weld: Performing the second-level welding process.
- Vision: Carrying out a vision project to check the weld integrity.
- Resistance Test: Conducting electrical resistance testing process.
- Nak and Eject: Applying hacks to the body of the piece.
Additional description of station
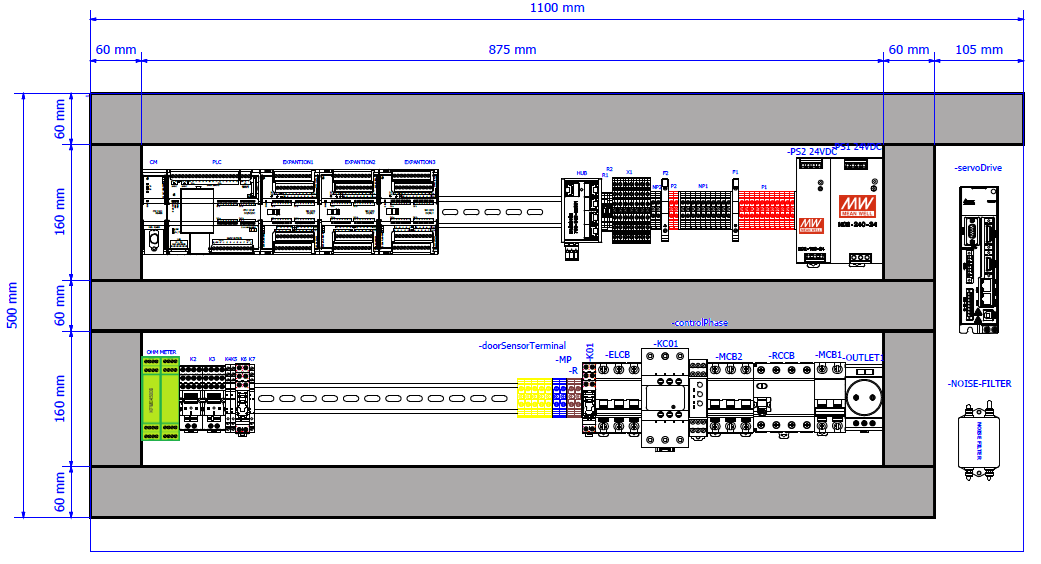
Explain the details
- Siemens controller s1200 1214 DC/DC/DC.
- motion control with PWM siemens module.
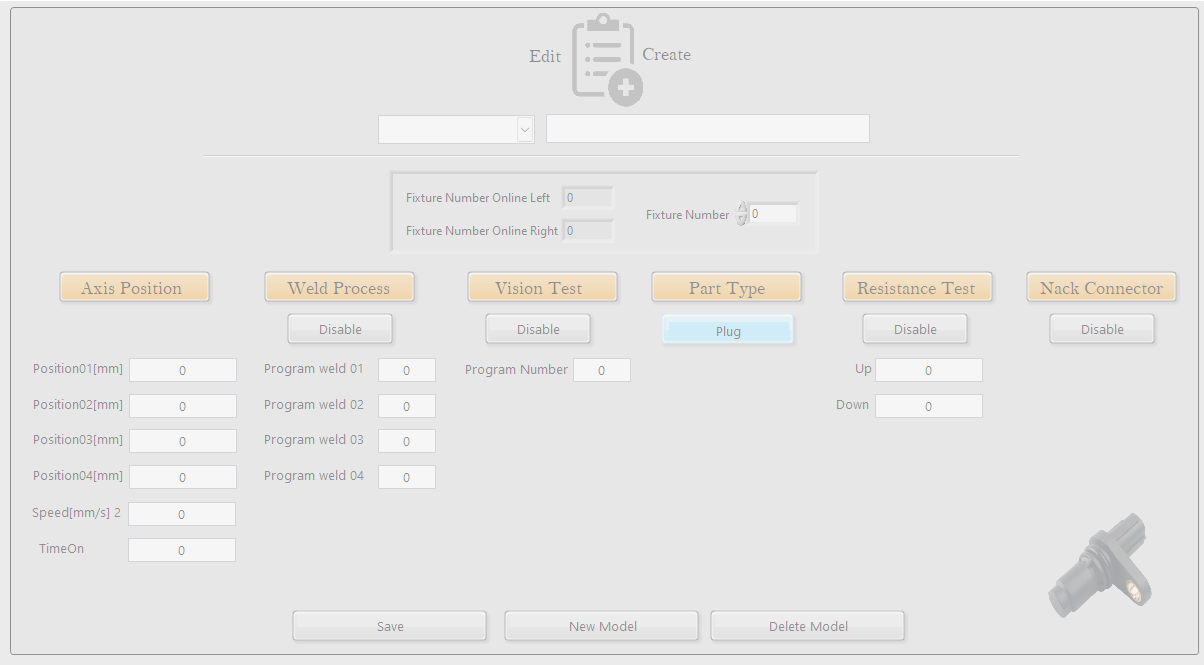
Software accesses
- Ability to determine multiple precise positions for spot welding
- Determine a separate welding program for each point
- Ability to determine the Vision Process program number
- Ability to determine the type of sensor "wired, wireless"
- Determine the resistance range of the test item
- Ability to activate and deactivate each process
- Ability to connect to the SQL database
- Ability to save information related to the manufactured material
- Ability to print barcodes generated from the central SQL database
- Ability to precisely adjust the printer to insert the desired information
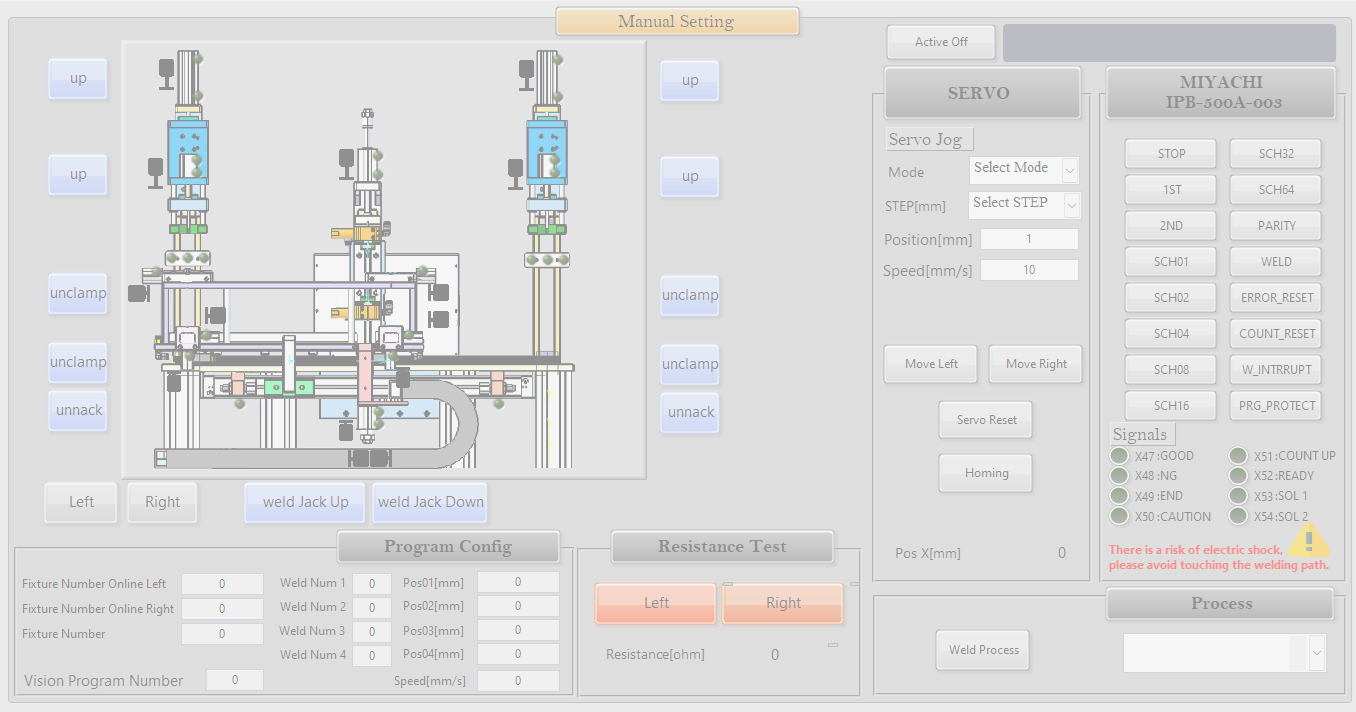
Device Manual Settings
- Ability to test the performance of each part
- Ability to view feedback on the performance of each part
- Ability to adjust the axis position to select the welding position
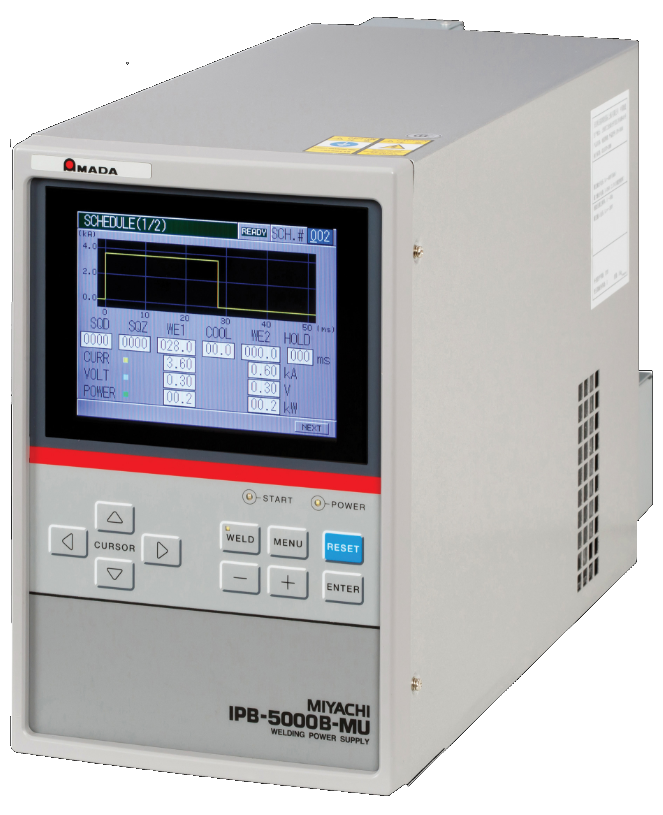
ٌWelding Machine
- AMADA WELD TECH IPB-5000A.
- AMADA WELD TECH model IPB-500A.
- Number of weld schedules: 127
- Time settings: Squeeze delay: 0 ~ 600 ms
- Time settings: Squeeze: 0 ~ 600 ms
- Time settings: Weld 1, 2: 0 ~ 600 ms
- Time settings: Up slope: 0 ~ 600 ms
- Time settings: Cool: 0 ~ 600 ms
- Time settings: Off: 0 ~ 600 ms
- Maximum secondary current: 3000A (5%)
- Secondary voltage, no load: 9 V
- Time settings: Off: 0 ~ 600 ms
- Application: 1-Fusing of tunic covered wires
- Application: 2-Welding of terminal and stranded wire