Hot Plate Welding
Step One
Part halves are placed into and securely gripped by precision holding fixtures which insure adequate support and accurate alignment of the part halves throughout the hot plate welding process.
Step Two
To heat the part joint area, a thermally heated platen is placed between the part halves. The holding fixtures close to compress and melt the part halves to be welded against the platen, displacing material at the joint area only
Step Three
Compression and material displacement continue until precision hard-stops built into the tooling are met. Thermal heat continues to conduct into the material even though compression and displacement have stopped.
Step Four
After the joint area reaches molten temperature, the holding fixtures open and the heat platen is withdrawn.
Step Five
The holding fixtures then close, forcing the two parts together until hard-stops on the holding fixtures come into contact with one another.
Step Six
When cooling is complete, the gripping mechanism in one of the holding fixtures releases the part, the holding fixtures open and the finished part may be removed.
Car dashboard door welding
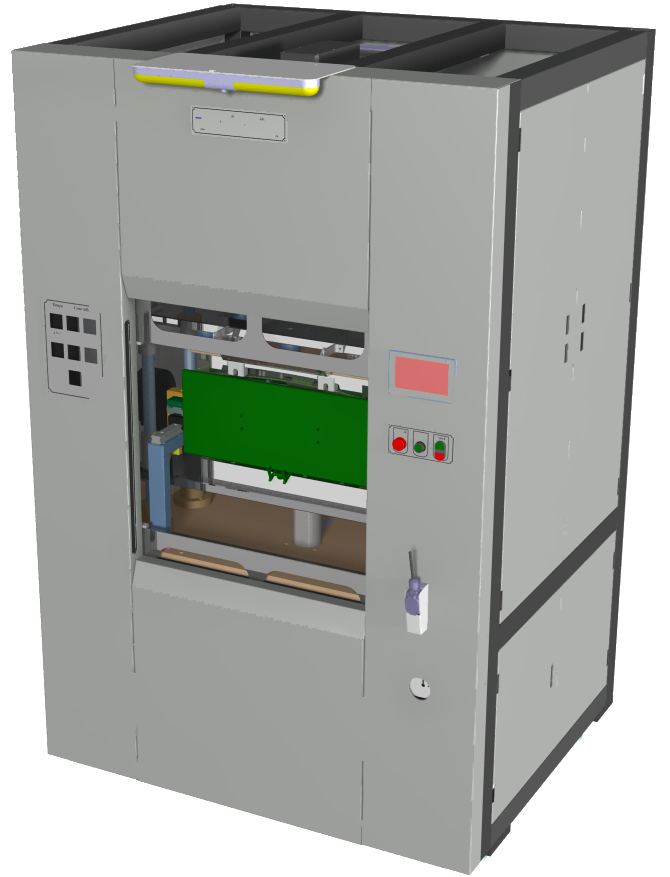
The controller of this device is motion controlled, it has the ability to program 200 different modes.
The movement accuracy is 0.04 mm and the production cycle time is 74 seconds.
The cooling system of the welding area that works locally.
It has multiple temperature settings for spot melting of the hot plate.
Mechanism and internal view of the device
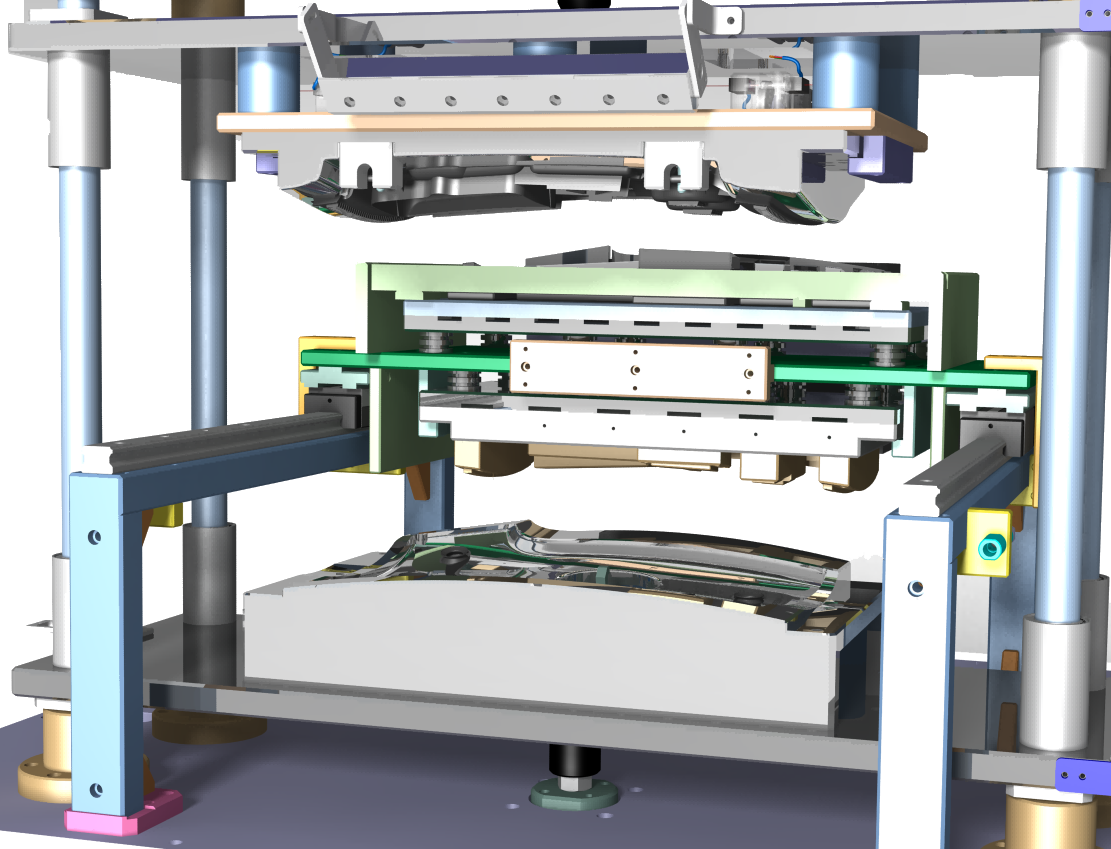
The controller is TexComputer, which moves the hot plates by ball screw, jack slide is used to transfer the product. A vacuum was used to hold the part
Multiple hot plate
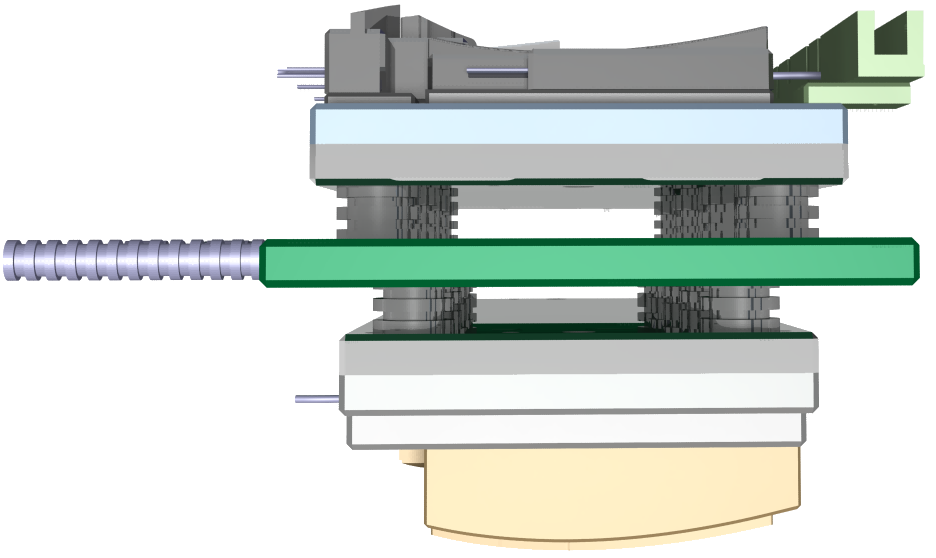
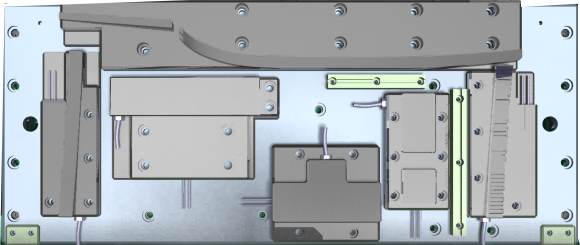
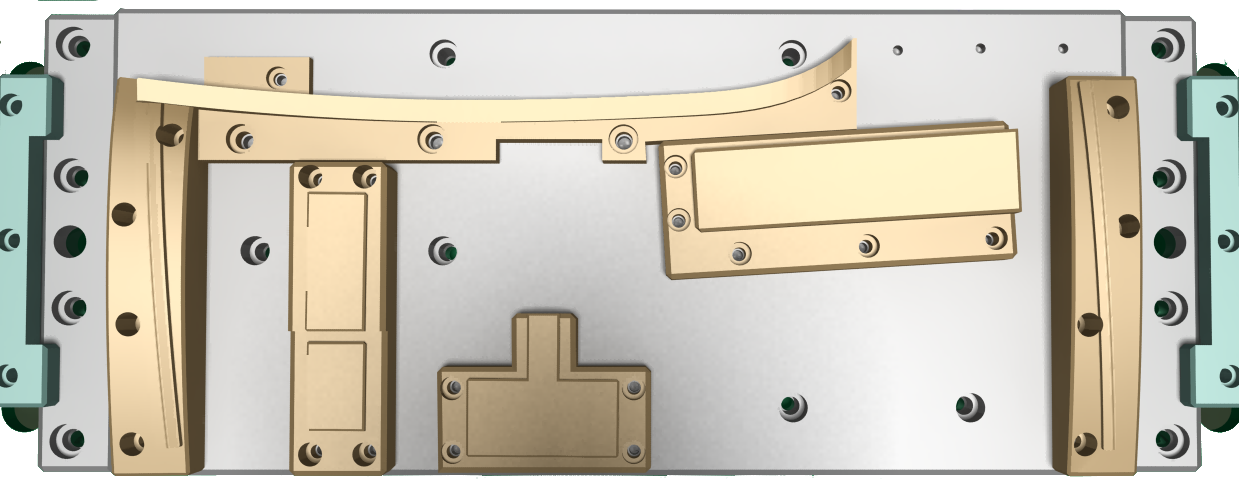
It has a separate temperature control system, which increases the welding quality.