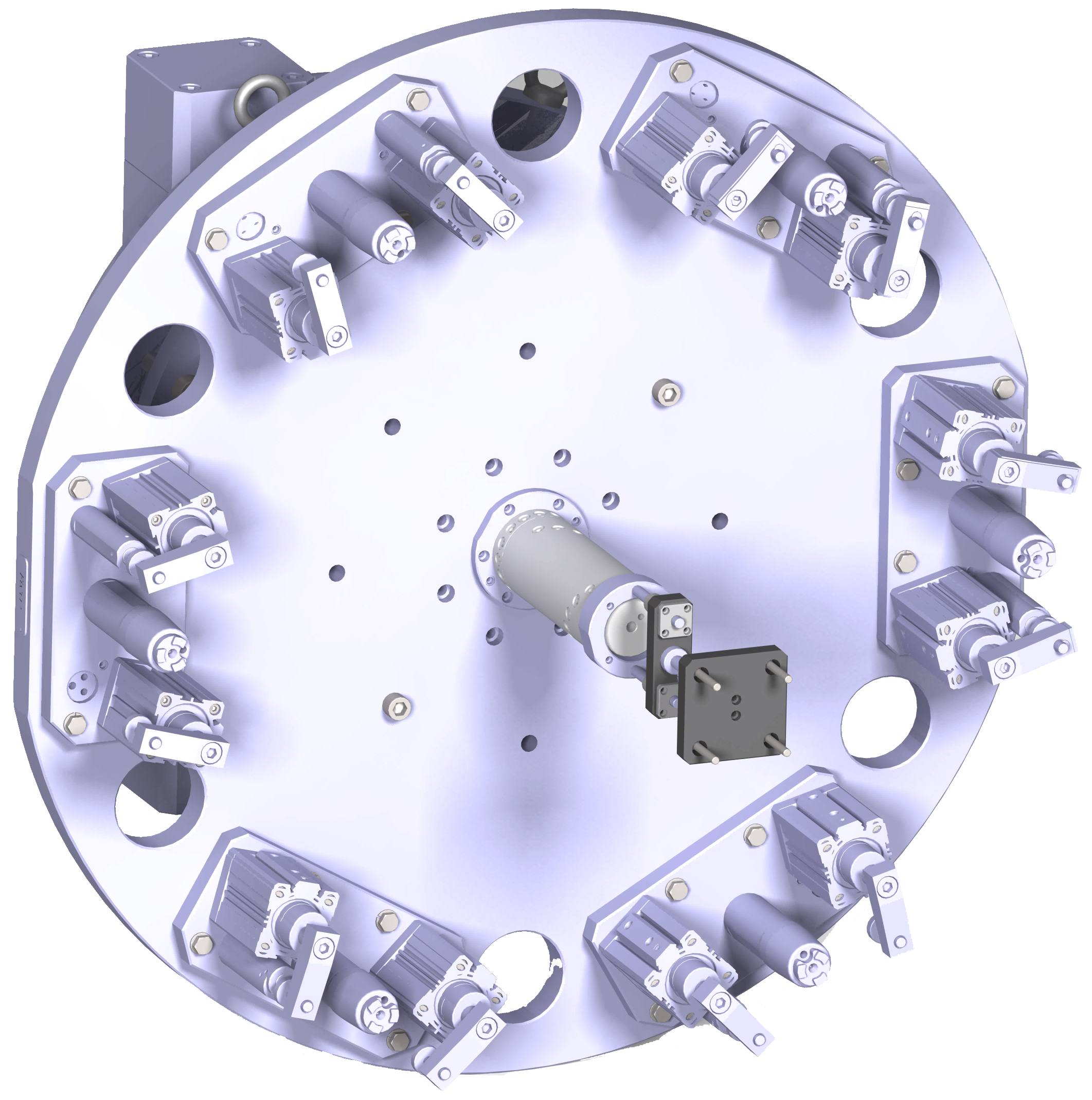
Milling Car Caliper
Description
Caliper Brake Hole Drilling and Threading Machine
This machine is designed for the precise drilling and threading of automobile brake calipers. It performs a complete cycle in five stages: drilling, threading, washing, and part ejection. The machine boasts an production cycle time of just 25 seconds, highlighting its efficiency and precision.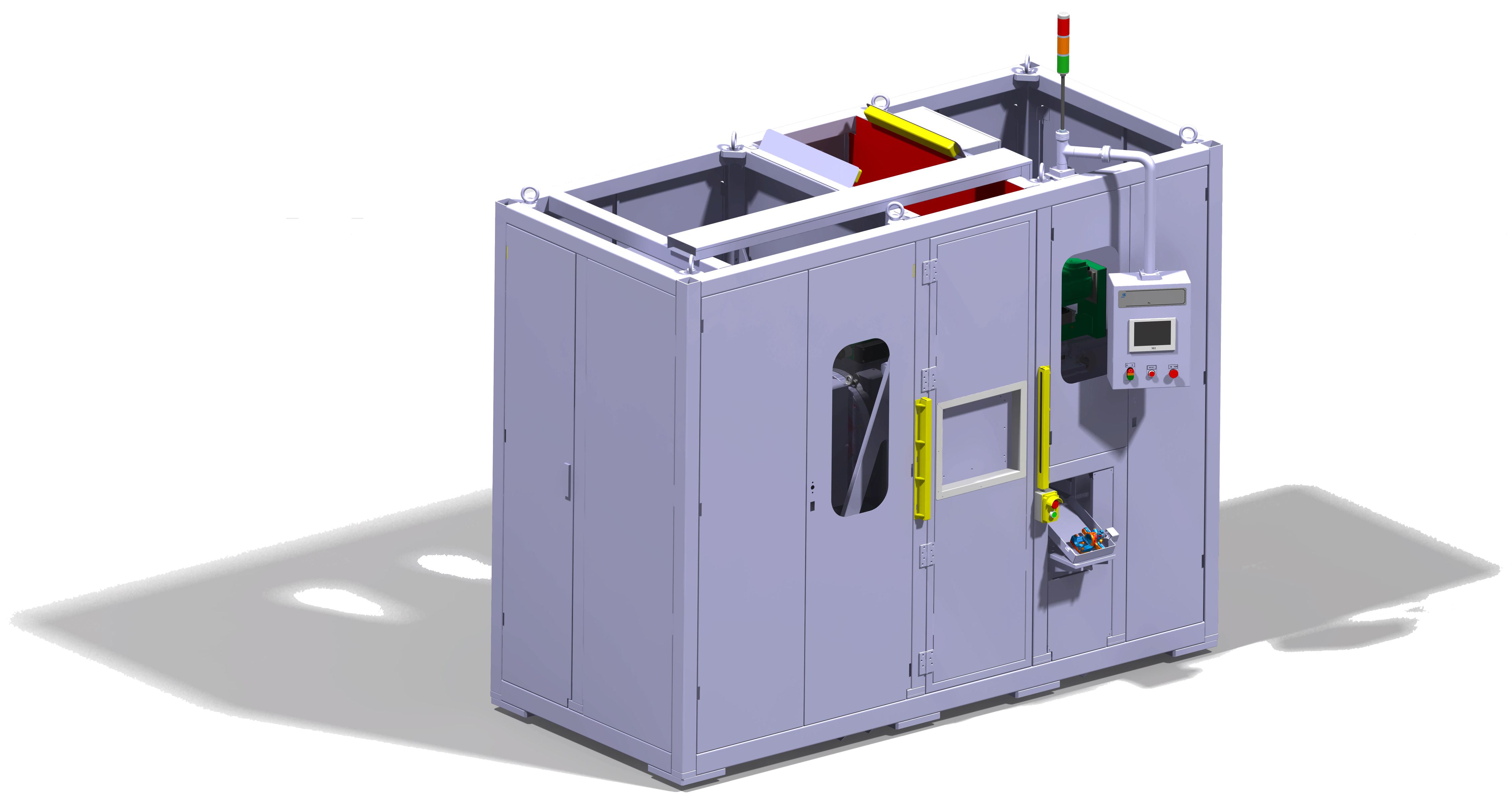
Stages of the work cycle
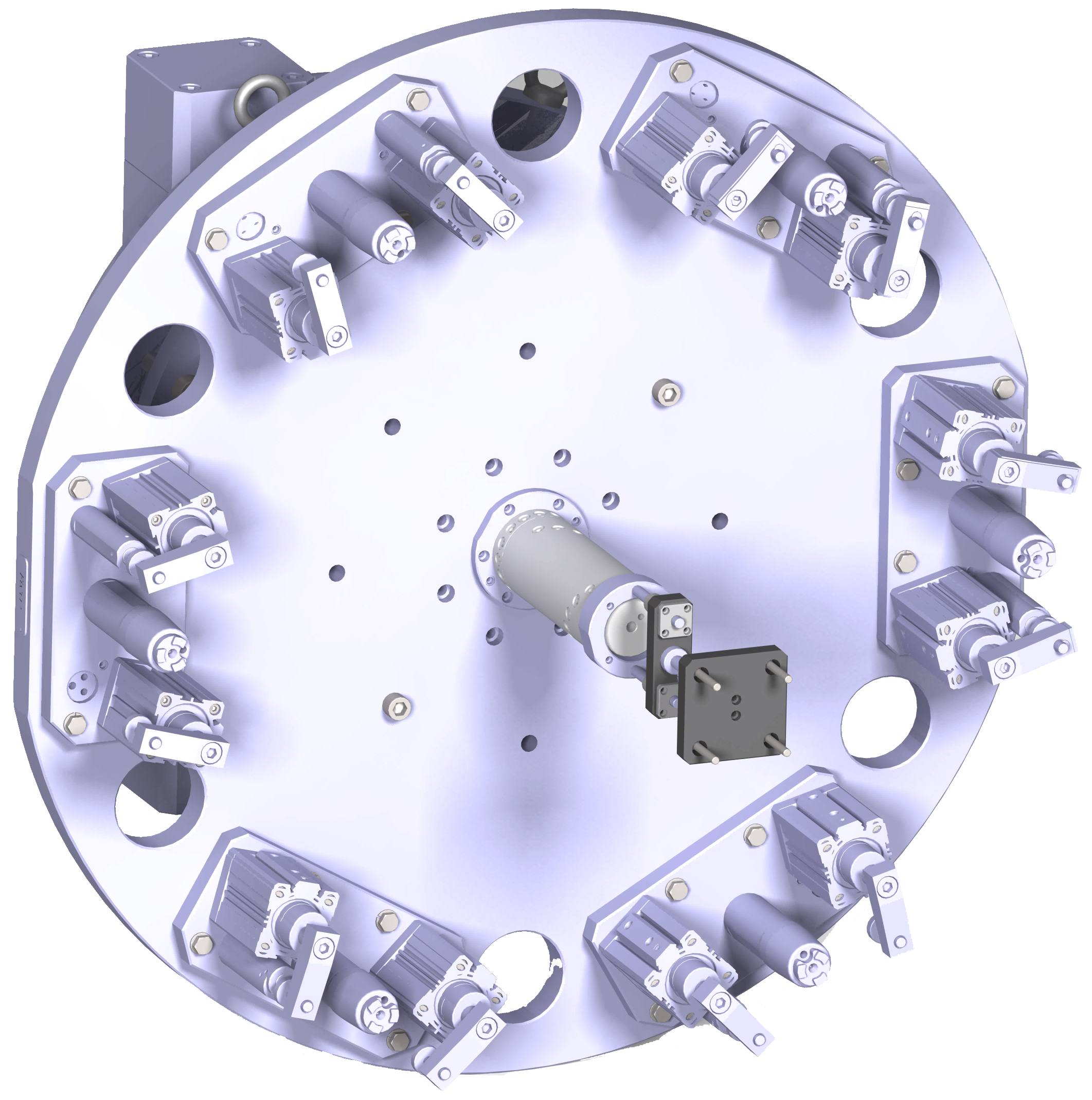
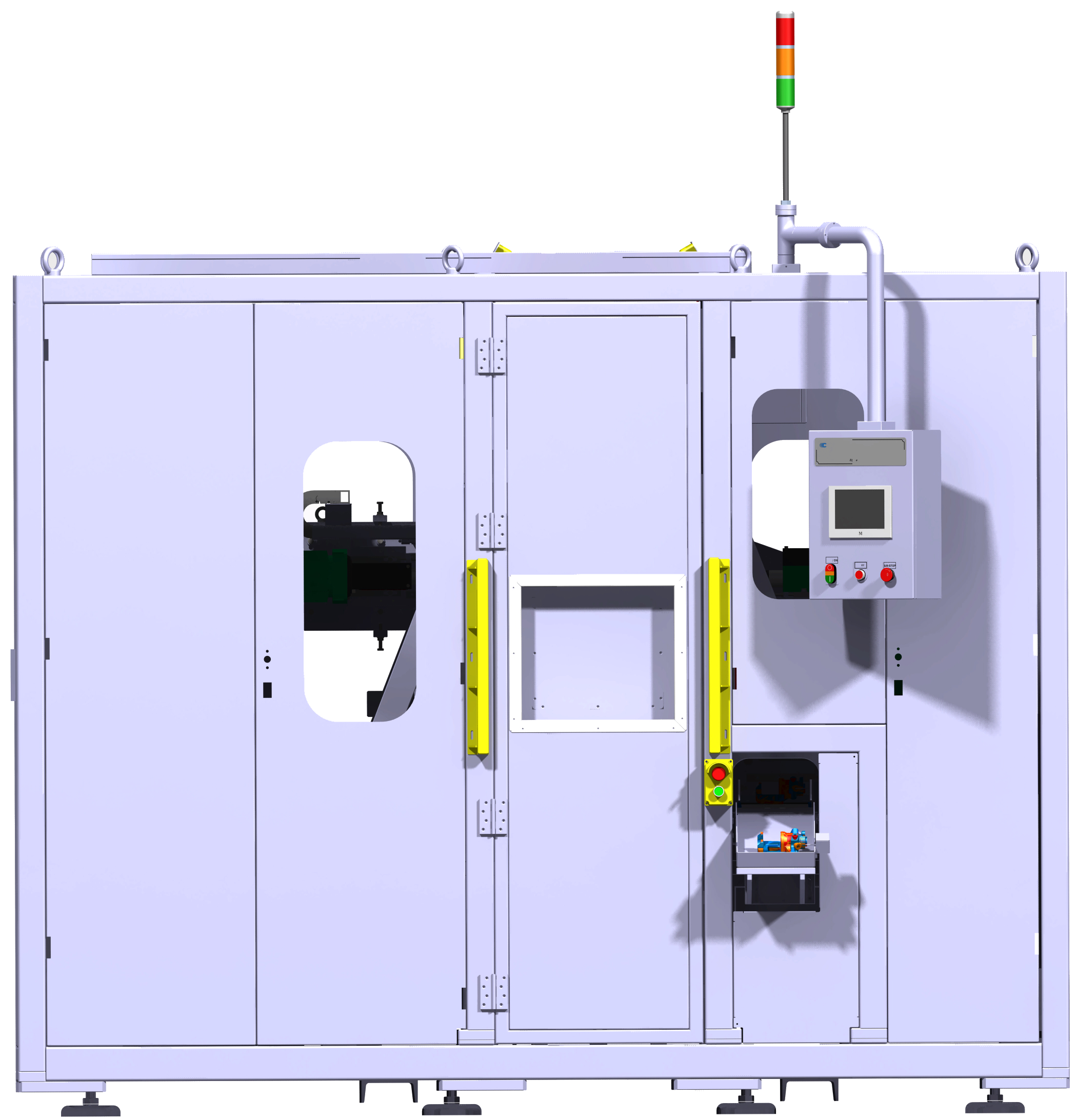
- Insert Part: The part is placed by the operator. The start key is pressed by the operator.
- ٍEjact Part: The piece is removed from the machine by the conveyor, and the conveyor waits to pick up the piece.
- Index: All index fixtures have jack clamps.
- stage 01: In order to detect the presence of the part and also to place the part correctly in the fixture, a jack with LVDT performs diagnosis and correction.
- check tools: In all drilling and threading stations, the presence of tools is checked.
- stage 02: In this station, the piece is drilled by the spindle.
- stage 03: In this station, the piece is drilled by the spindle.
- stage 04: In this station, the part is threaded by the spindle.
- stage 05: In this station, the part of the automatic system is transferred to the conveyor.
- stage 06: Fixtures are washed at this station.
Additional description of station
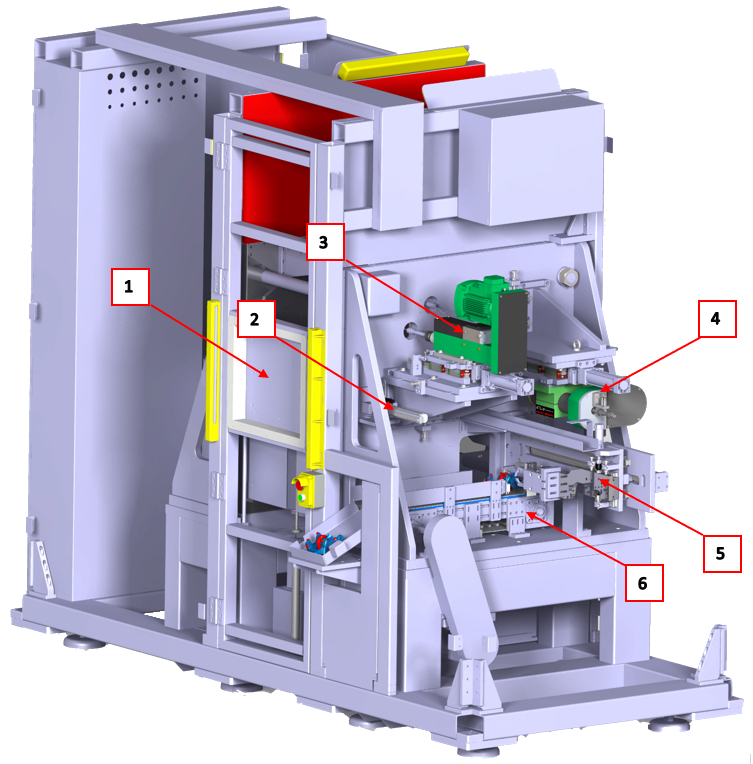
Explain the details
- Automatic door with light curtain protection system.
- Part placement system and placement accuracy detection tester.
- Drilling system of station 03
- threading system of station 04
- Part conveyor system of station 05
- Conveyor transmission system
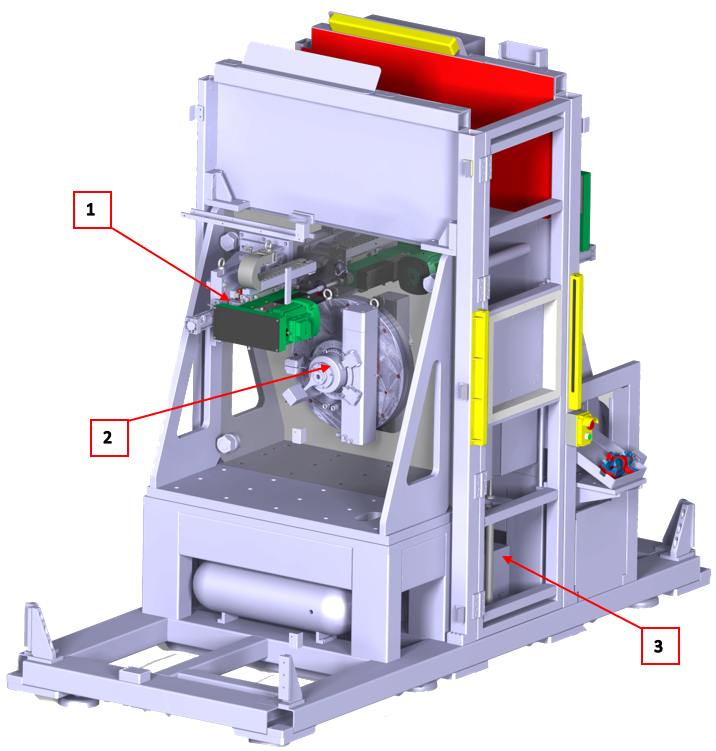
Explain the details
- Drilling system of station 02
- Index system
- Soap and water system
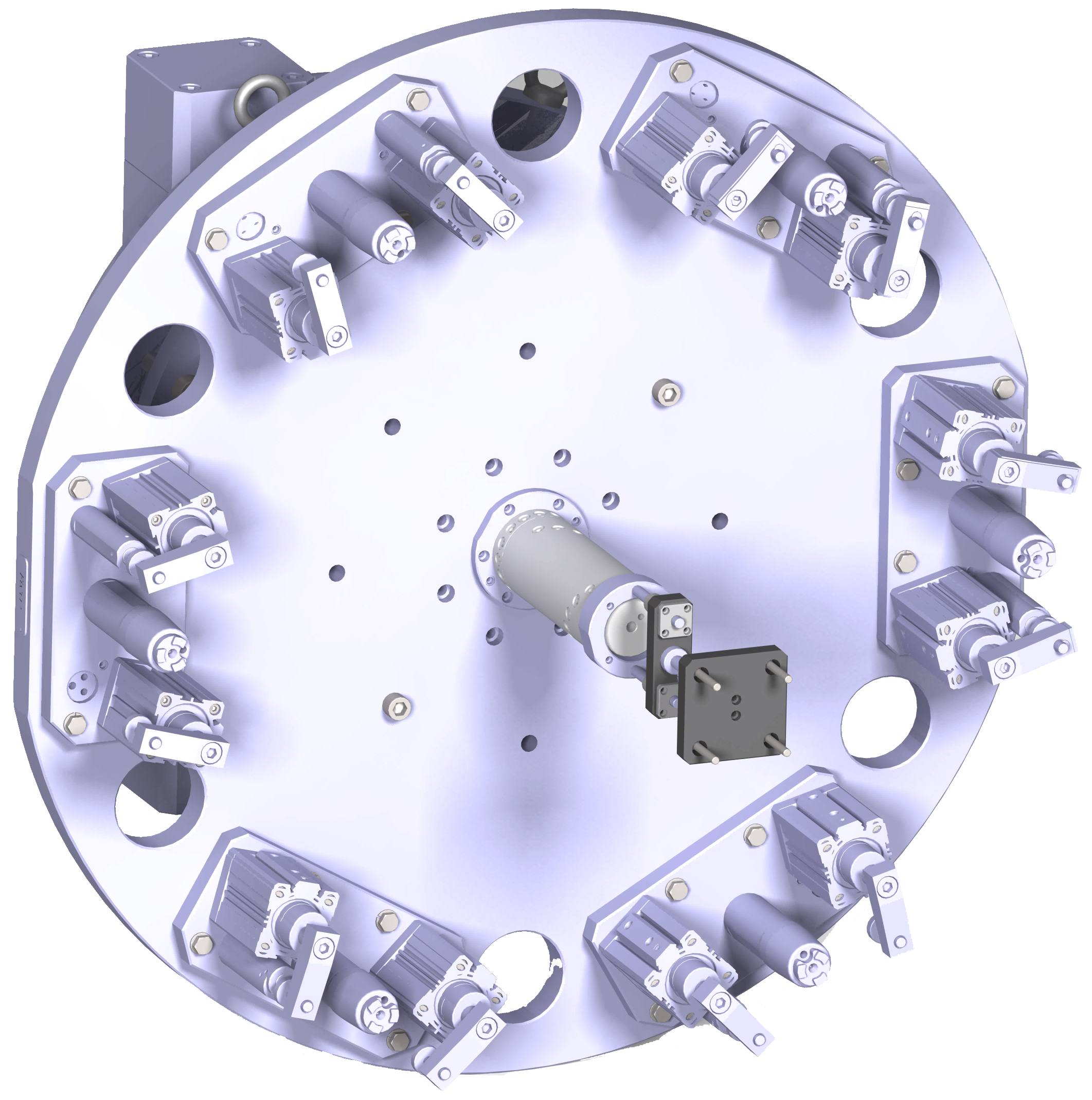
Explain the details
- It has six fixtures.
- Each fixture has two jack clamps.
- The pneumatic system of rotary clamp jacks.
- The rotation system of the index plate is based on hydraulics and starts rotating with 60 bar pressure. After each rotation, the index plate is locked by the hydraulic system.
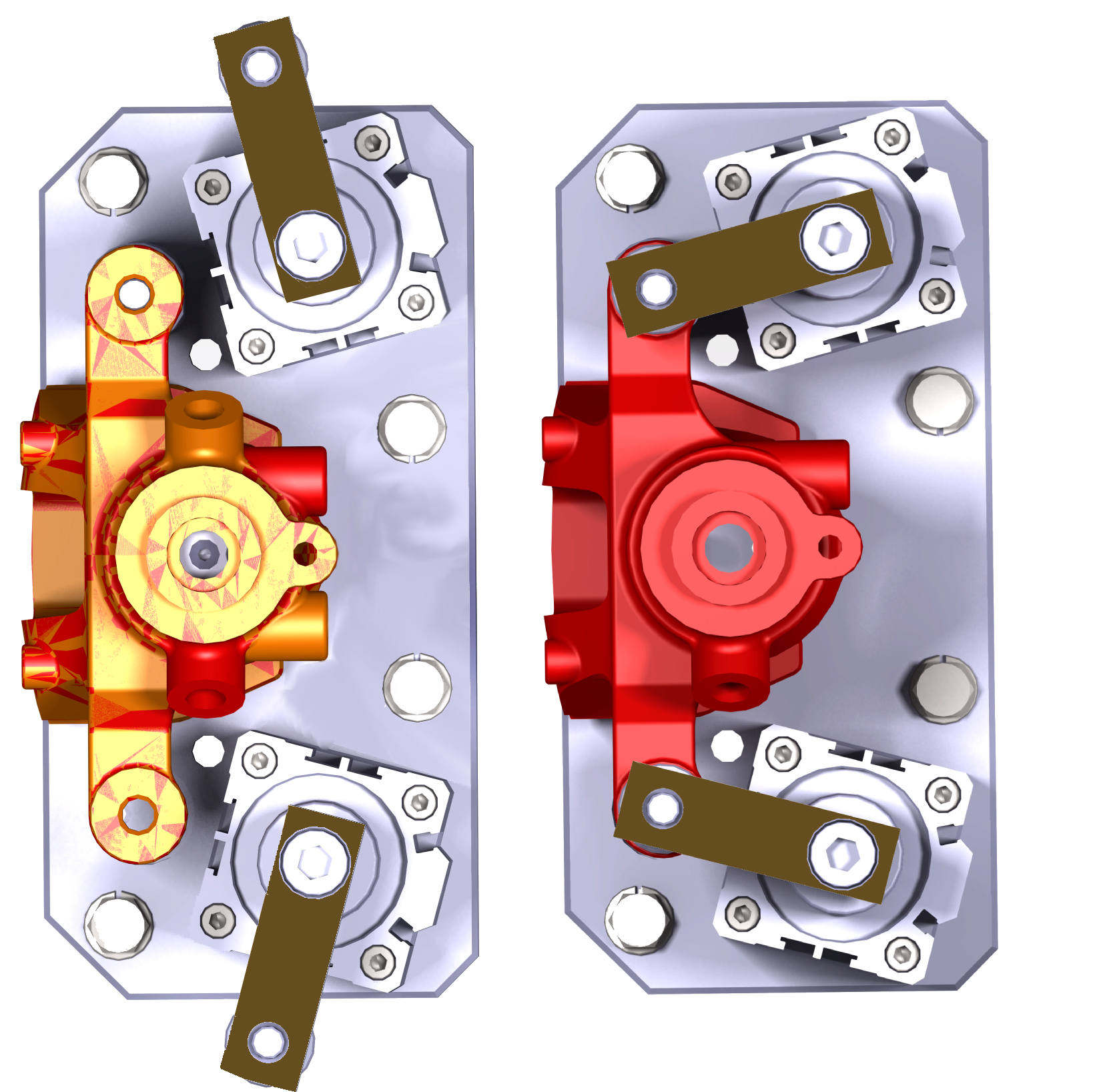
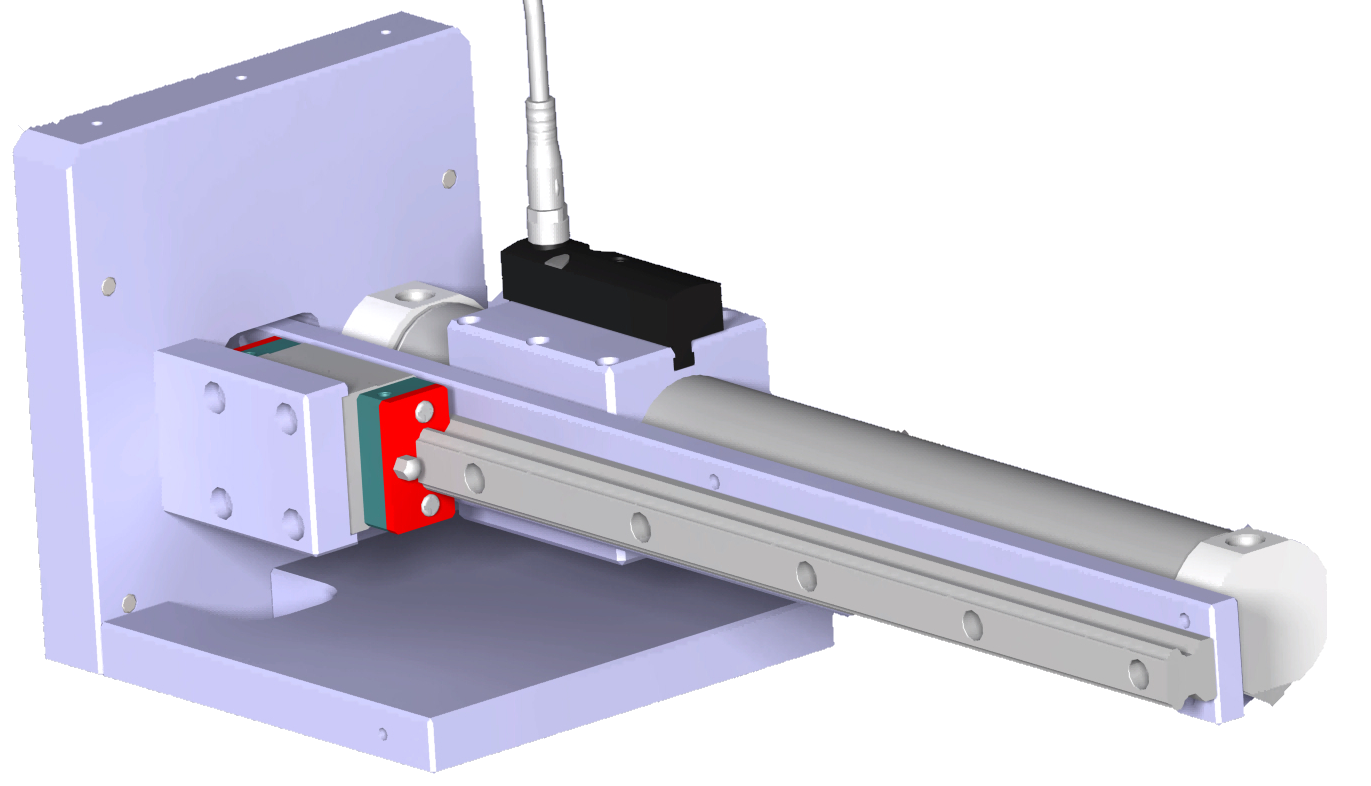
Explain the details
- There is an LVDT on the jack that detects the exact position of the jack.
- SMAT-8E-... Position transmitter
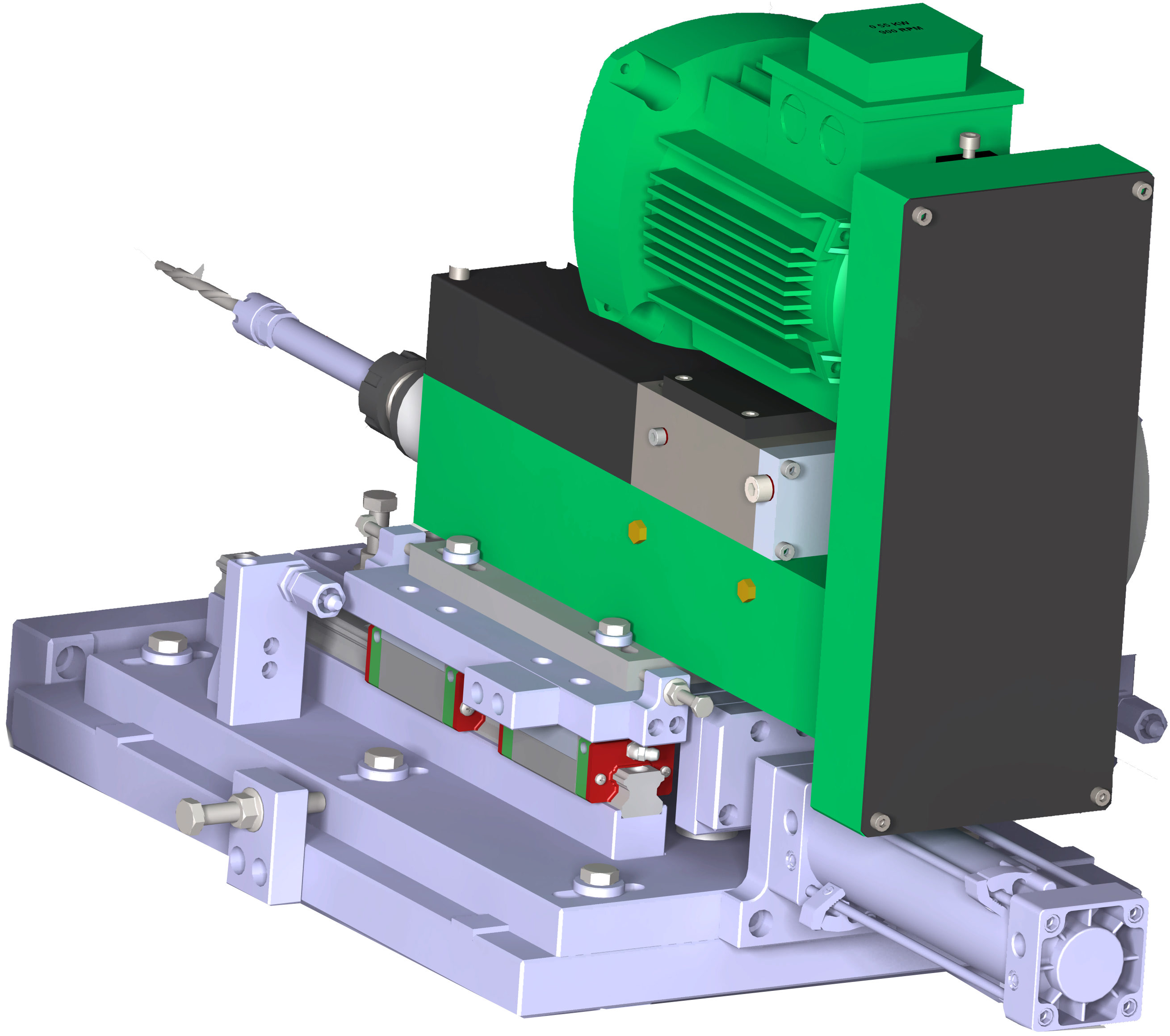
Explain the details
- The spindle is located on two jacks.
- First jack: high speed and high movement course.
- Second jack: low speed with low movement course.
- 3000 rpm spindle with 800w power was started with LS driver.
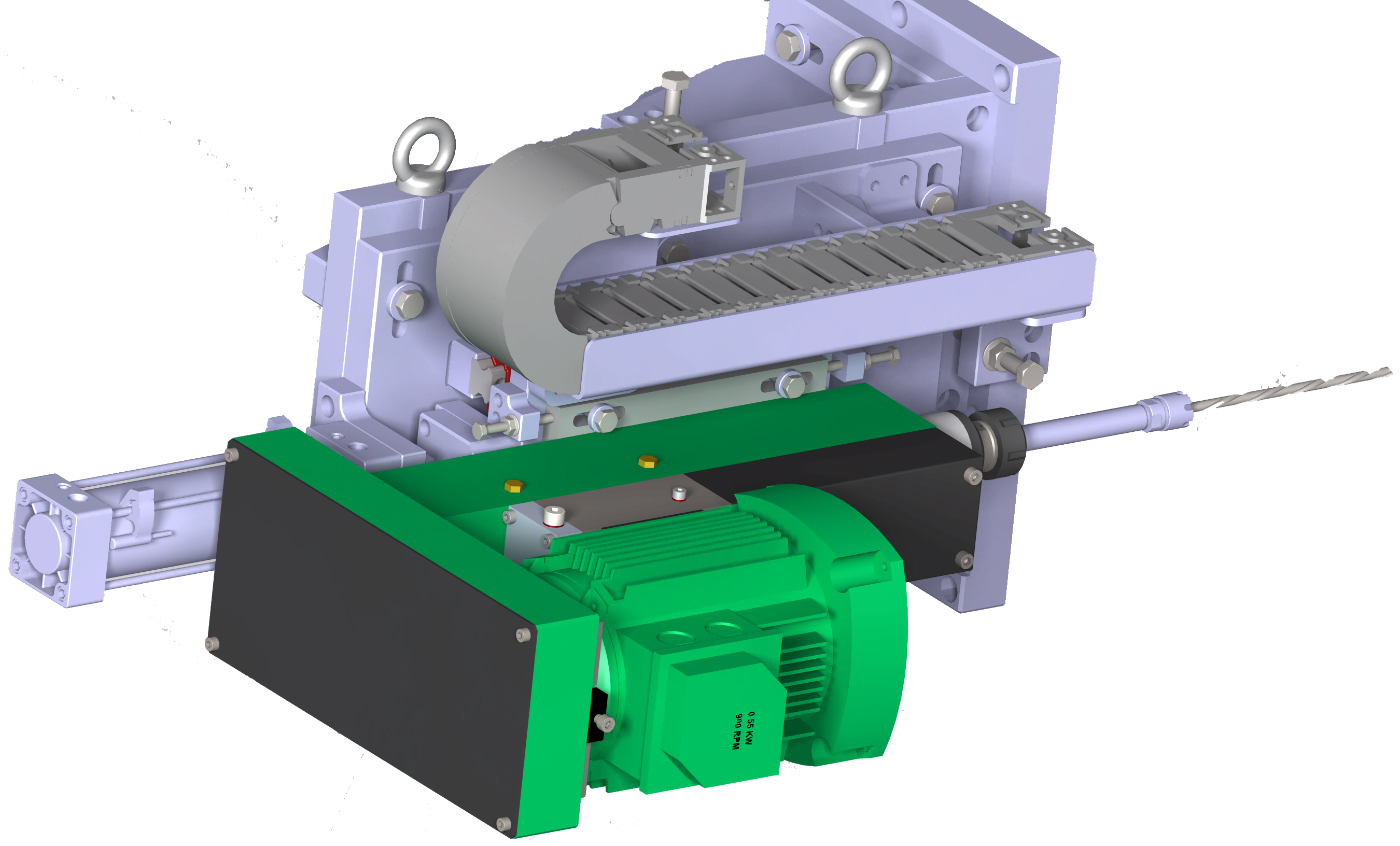
Explain the details
- The spindle is located on two jacks.
- First jack: high speed and high movement course.
- Second jack: low speed with low movement course.
- 3000 rpm spindle with 800w power was started with LS driver.
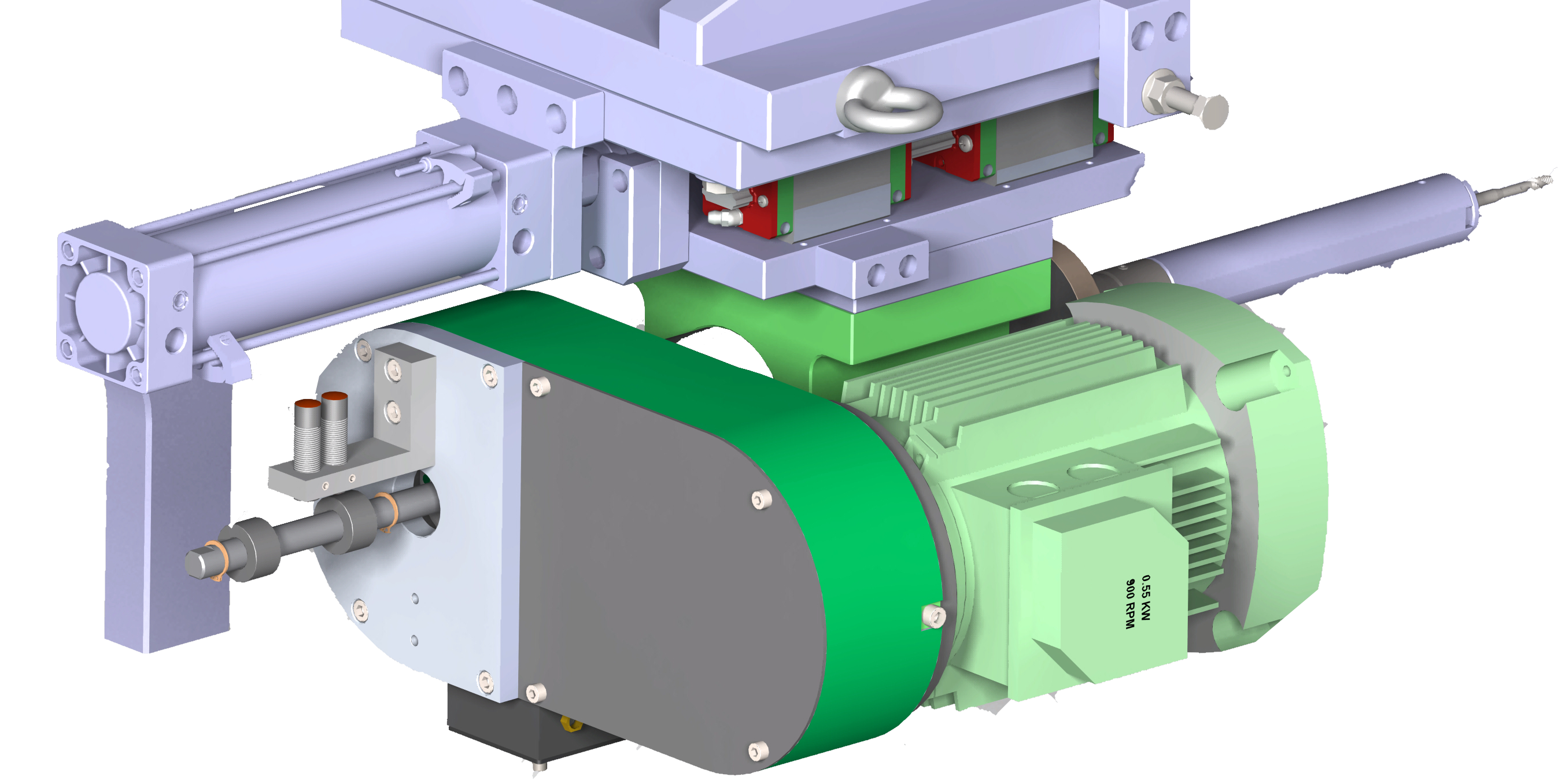
Explain the details
- The spindle is located on two jacks.
- First jack: high speed and high movement course.
- Second jack: low speed with low movement course.
- 3000 rpm spindle with 800w power was started with LS driver.
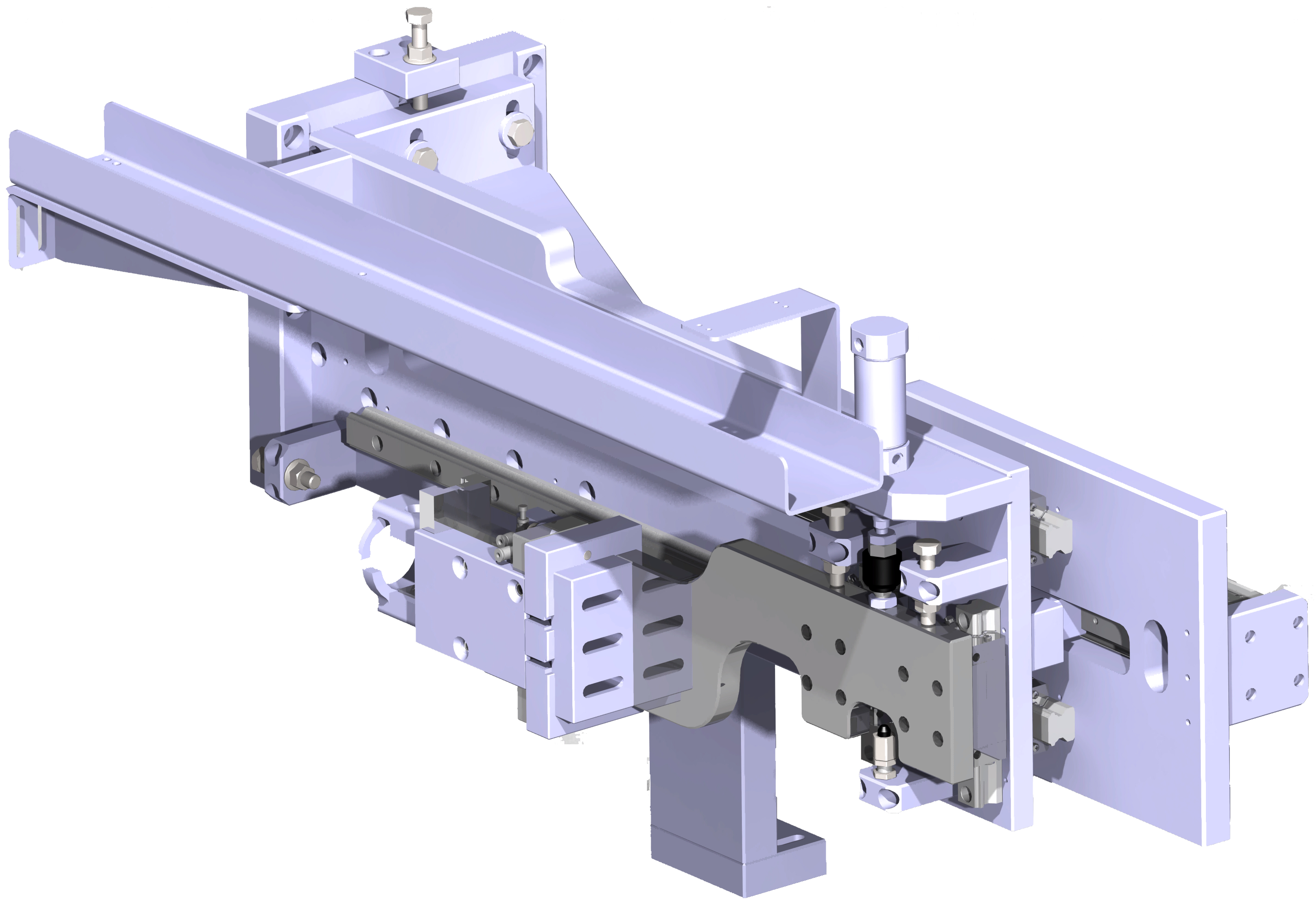
Explain the details
- It is moved by three moving jacks in X and Z axis and a jack gripper.
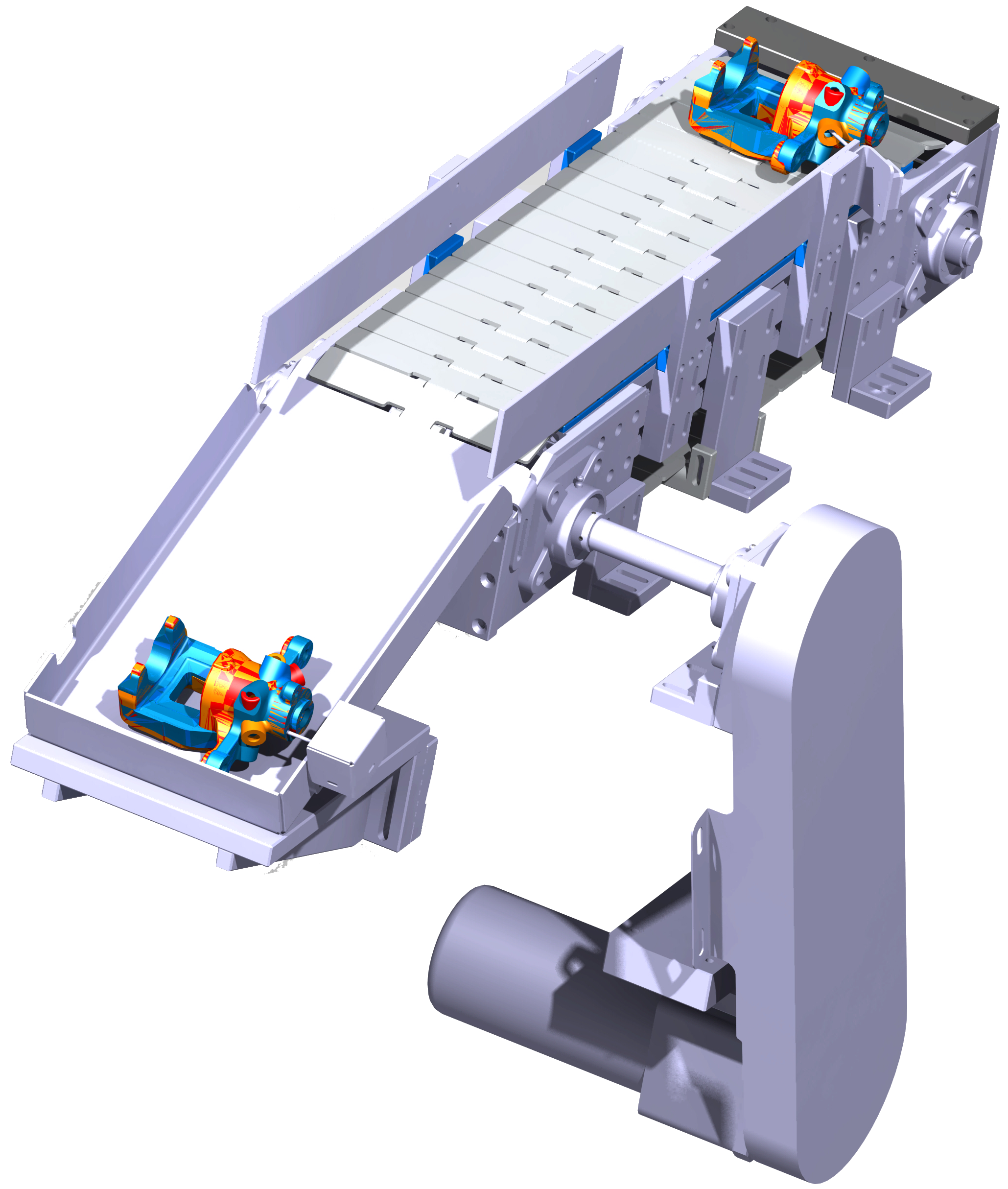
Explain the details
- The presence of the piece is determined by two ultrasonic sensors.
- 3000 rpm spindle with 450w power was started with LS driver.
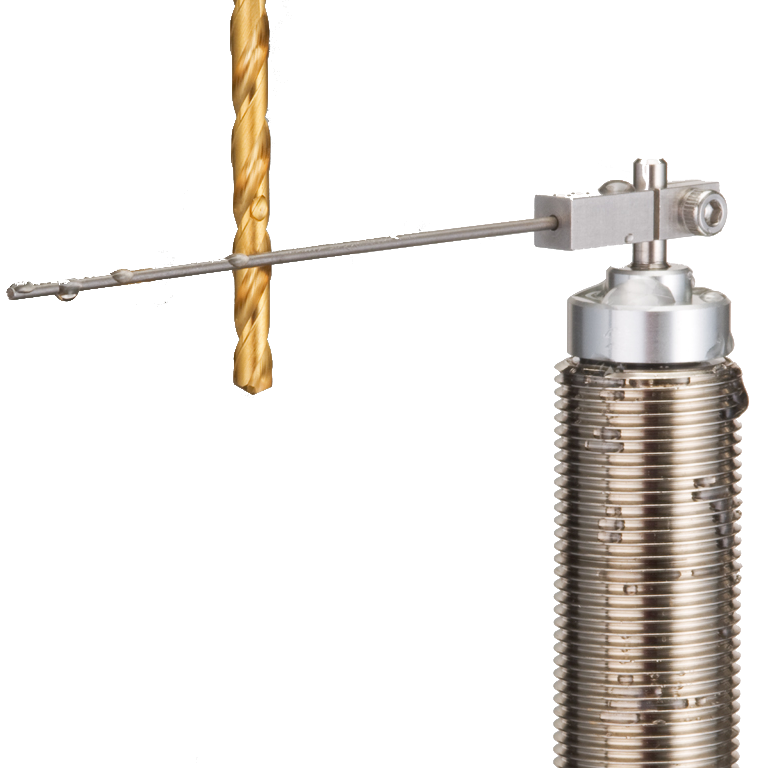
Tools Check
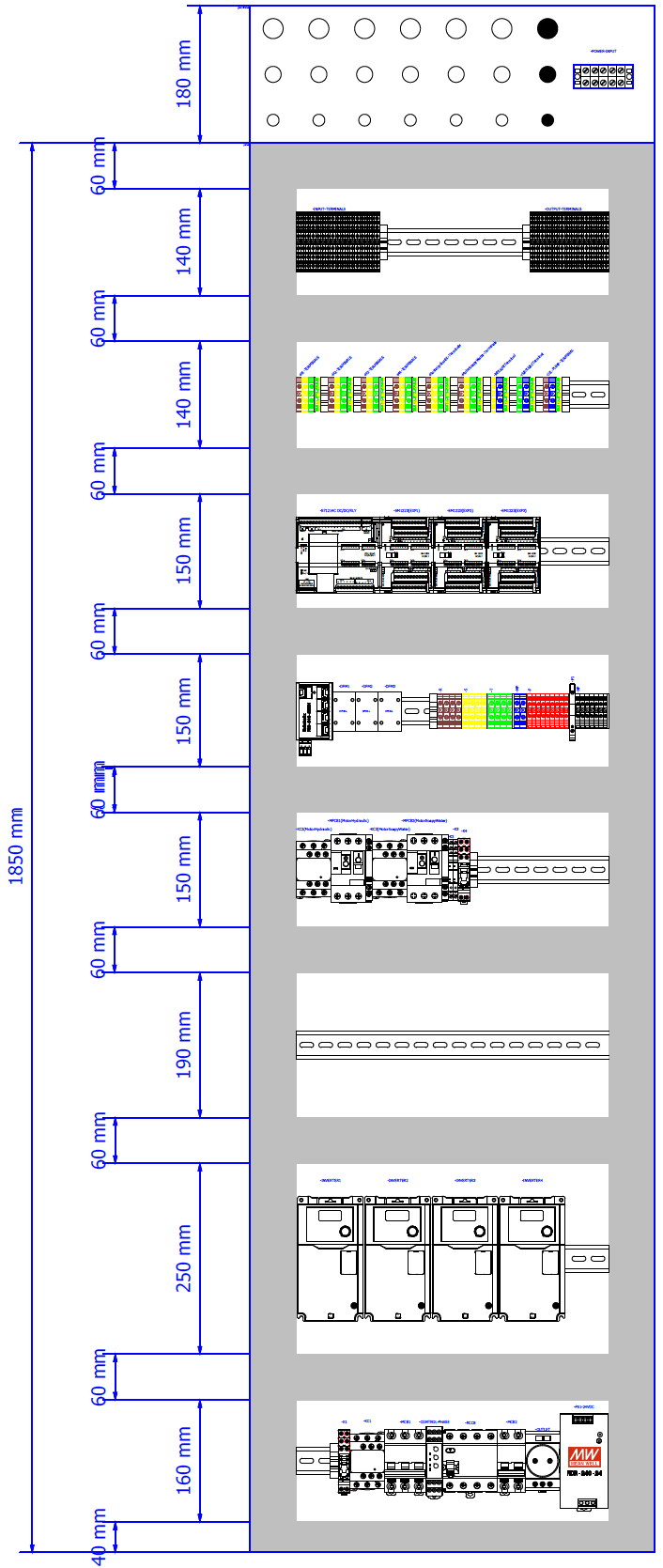
Electrical Panel
- The electrical panel has IP 56 to prevent the penetration of soap and water mist.
- Siemens plc SIMATIC S7-1200 1214C AC/DC/Relay 6ES7214-1BG40-0XB0.
- Siemens Module SIMATIC S7-1200 SM 1223, 16 DI/16 DO RLY 6ES7223-1PL32-0XB0.
- Driver motor LS.
- metrol sensor Driver.
- vortex cooling is used for cooling inside the electrical panel.
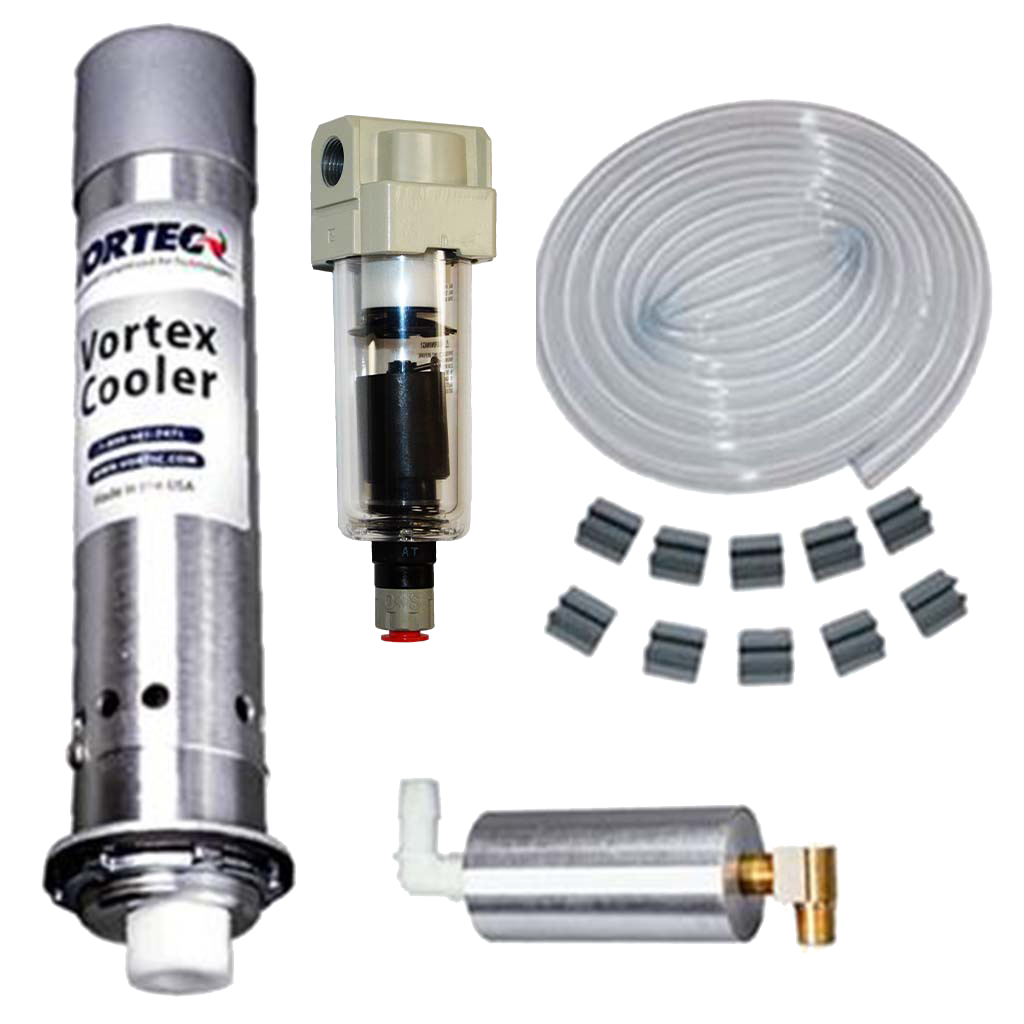
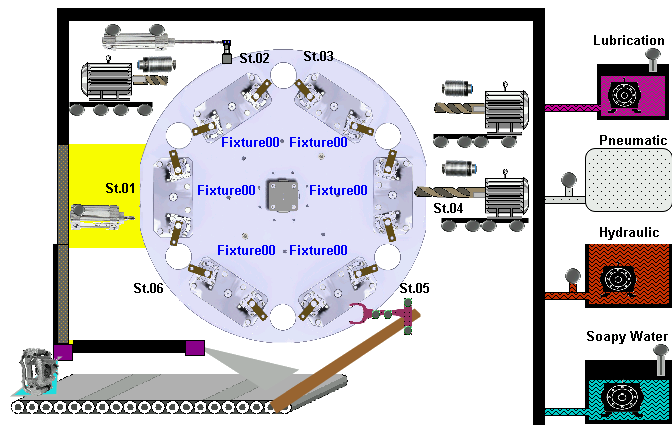
Software details
- Ability to enable/disable the function of each fixture.
- Ability to determine the model of each fixture.
- Ability to enable/disable the function of each station.
- Ability to enable/disable the function of each check tools.
- Login system and standard access level.
- It has functional memory in each station for better and more accurate performance.
- Show the performance of different parts of the device.
- Simultaneous operation of stations